Peter Tsai may not be a household name, but odds are you know his work.
The recently retired research faculty member of Material Sciences is the architect behind the essential technology in N95 respirators. These respirators are required by OSHA when working in dusty environments to remove at least 95% of submicron particles, and recommended by the World Health Organization to protect against SARS, bird and swine flu, and other airborne diseases. The University of Tennessee’s world-renowned expert in nonwoven fabrics has 12 U.S. patents and over 20 commercial license agreements and counting under his belt. In the last six months alone, UTRF has non-exclusively licensed his most recent technology to four companies globally.
In the world of nonwoven fabrics, Peter specializes in two broad areas: electrostatic charging, in which permanent charges are embedded into a fiber to form an electret that enhances filter efficiency by electrostatic attraction, and melt blowing, a nonwoven process that makes microfibers into a fabric by scattering a polymer resin at a high air velocity. His research has not only advanced the efficiency and application of nonwoven fabrics but has revolutionized the electrostatic charging and melt blowing processes themselves.
Peter’s partnership with UTRF spans more than 25 years. In 1995, he received five U.S. patents, including one for the corona electrostatic charging of nonwoven fabrics technology – the key component in the aforementioned N95 respirator. Peter’s novel method uses an electric field to ionize the neutral air to generate ions and electrons, which then charge the nonwoven fibers through field and induction. Using his innovative approach, the charged nonwoven fabric can filter particles in the air ten times more efficiently than uncharged fabrics without adversely increasing the air resistance. In addition to respirators, Peter’s technology has been widely used by industries for over three decades in products such as HVAC filters and medical face masks.

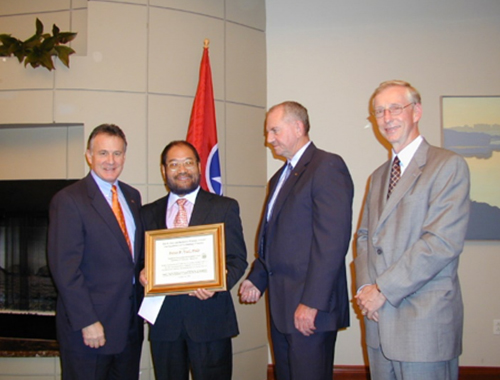
Just last year, Peter developed a new approach to apply electrostatic charge to fabrics through friction. His new technology involves saturating nonwoven fabrics with extremely pure water, which he then draws out using a high-pressure vacuum. This process, called hydro triboelectrification, generates friction and conveys the charge on the fabric so efficiently that the process need not be repeated. The resulting nonwoven fabric boasts a filter efficiency 20 times greater than that of untreated fabrics.
In recognition of his direct and active role in the commercialization process, Peter received the 2006 B. Otto and Kathleen Wheeley Award for Excellence in Technology Transfer. The Wheeley Award is UTRF’s most prestigious honor, given to a UT employee who excels in the commercialization of university-based research.
“Peter exemplifies how UT researchers can have a huge impact on bringing innovative products to market by making and maintaining valuable industry partnerships,” comments UTRF Vice President Maha Krishnamurthy. “We are grateful for his dedication to research and his passion and drive for the commercialization process.”
Devoted to his research in both theory and practice, Peter has declined many opportunities that would have required him to forfeit valuable time in his lab. His diligent commitment has paid off in spades for people around the globe: It’s estimated that more than one billion people have used Peter’s technologies to protect and improve their health.