UT researcher seeks to make glass fiber-based composites more sustainable.
Can the composites industry become more circular? One researcher from the University of Tennessee, Knoxville, is working to answer this question for fiberglass-based composites — which represent over 90 percent of the entire composites industry.
“There is a lot of push on carbon fiber recycling, which makes sense because it’s a very valuable material and is energy intensive to make,” says Ryan Ginder, research assistant professor in the Department of Mechanical, Aerospace, and Biomedical Engineering. “But to truly have a large impact on the sustainability of the composites industry, you have to figure out how to recycle glass fiber.”
To help tackle this problem, Ryan has developed a novel glass fiber recovery technology for large-scale recycling of wind turbine blades, and other glass fiber reinforced plastics, into new composites. His end goal is to take as much glass fiber composite as possible and divert it out of the landfill such that today’s wind blades can become tomorrow’s lighter weight, fuel efficient vehicles.
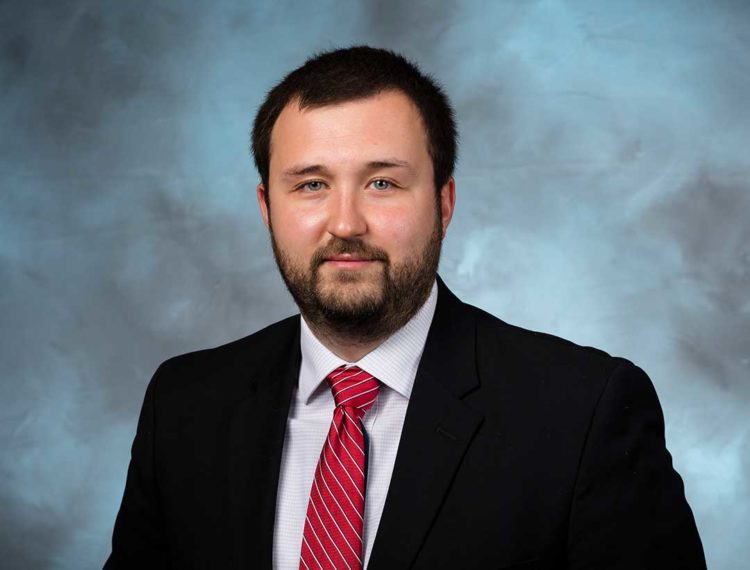
Like traditional recycling methods, Ryan’s technology uses heat to separate fibers from the various organic components present in composites. However, his technology modifies existing processes to mitigate thermal degradation and eliminate contaminants left behind during conventional processing. By eliminating these two problems, his technology results in a fiber that is mechanically intact and can be reused in future composites manufacturing.
Ryan recently received $1.1 million in funding from the U.S. Department of Energy’s Small Business Technology Transfer (STTR) program and Wind Energy Technologies Office to assist with further development and commercialization of his technology. Among his project partners is Carbon Rivers, a Knoxville startup founded by UT alumni to take advantage of market opportunities in advanced materials that will lead to a more sustainable and technology driven future.
Currently, Ryan and his team are in Phase II of the STTR. During Phase I, they transitioned from processing milligrams to kilograms. Now, they are working to scale up further from kilograms to a ton per day demonstration line. Carbon Rivers hopes to break ground on a commercial-scale facility in 2022, which would allow the team to process around 150 tons per day.
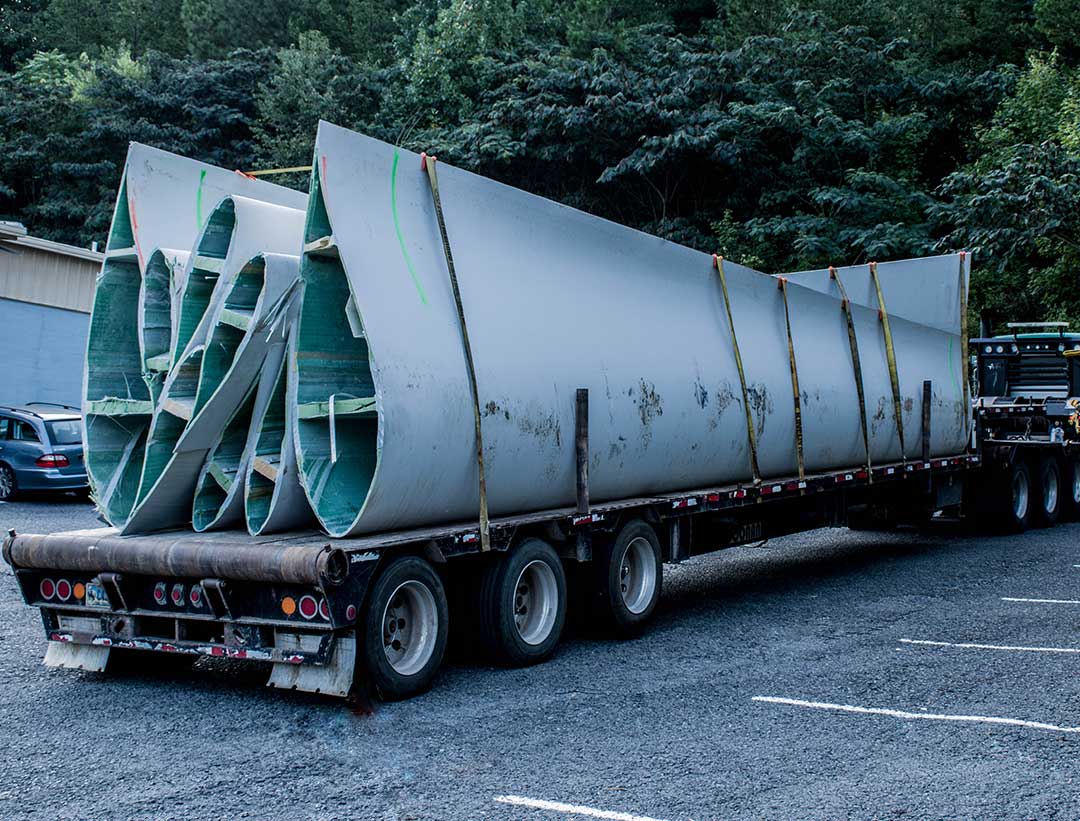
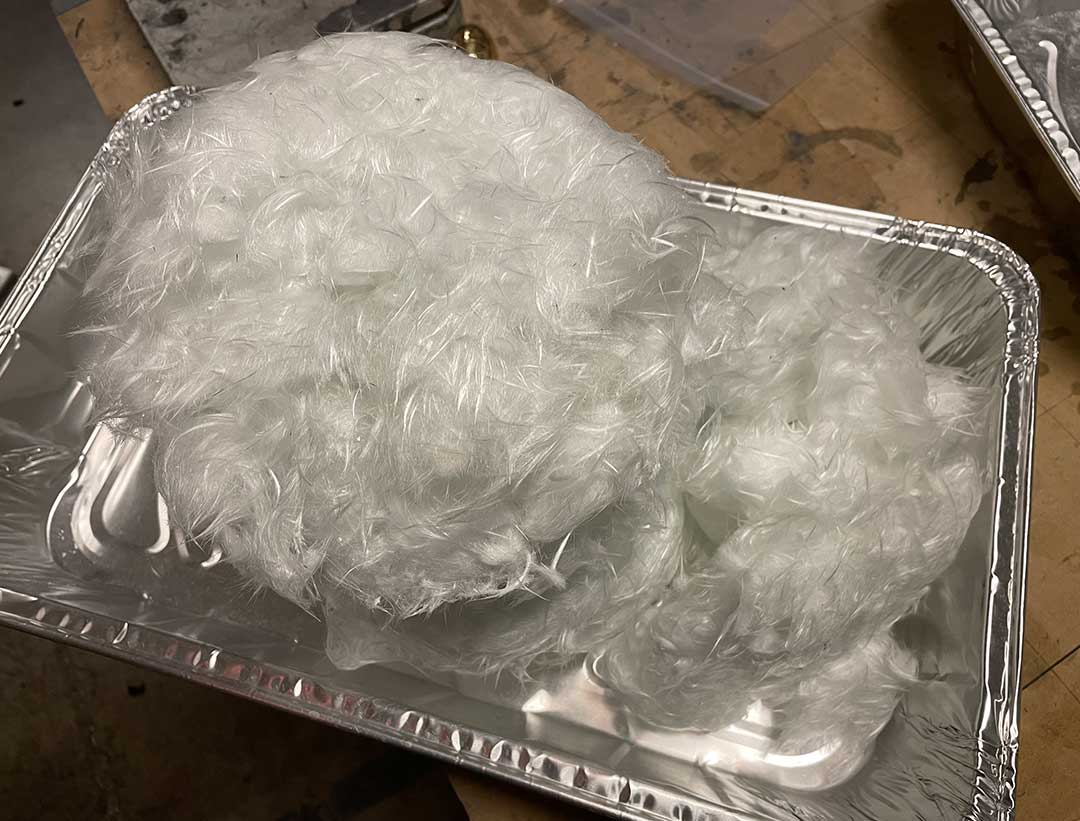
“Dr. Ryan Ginder and the Carbon Rivers team are working to make a lasting, sustainable difference in the composites industry as well as a positive impact on the environment by reusing materials that would otherwise end up in the landfill,” says Andreana Leskovjan, a technology manager at UTRF. “Ryan also thinks creatively about solutions to industrially relevant problems and finds the means necessary to pursue his goals.”
Ryan’s partnership with UTRF began when he filed the invention disclosure related to this technology in mid-2018. He has more recently worked with collaborators from BASF and ORNL on a production process for recycled carbon fiber automotive panels, which was disclosed to UTRF in 2019. In addition to his primary project, Ryan appreciates the opportunity to work with other UTRF inventors and technologies.
“I received a 2021 UTRF Technology Maturation Grant to look at an application area for some of the recycled fiber, which conveniently leverages two UT technologies,” Ryan comments. He is working with fellow UT alumnus and UTRF inventor, Hicham Ghossein of Endeavor Composites, to develop new composite materials for nonwoven fabric applications.
Outside of work, Ryan spends most of his time with his wife, three-year-old son, four-month-old daughter and his family’s two dogs and three cats — all Knoxville rescues.
“Between them and the kids, we have a pretty packed family life,” laughs Ryan.